Safety
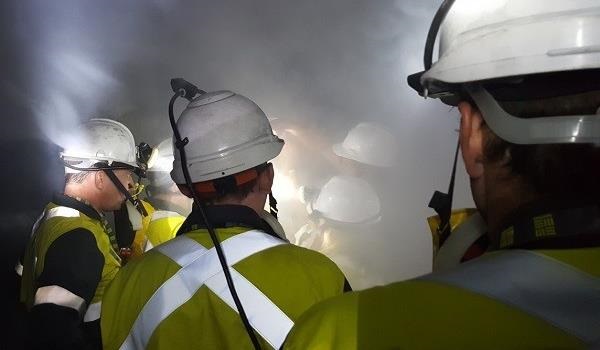
Our activities of mining, processing, refining and smelting present health and safety hazards which can have significant consequences if not appropriately addressed. Our health and safety approach seeks to identify and reduce the risk of exposure to these hazards and to create a healthy, safe and inclusive workplace for our people.
We are continuing to implement our global Safety Improvement Program, a multi-year program with the aim to achieve a step change in our safety performance.
The Program focuses on:
Read more about our Safety Improvement Program in our 2024 Sustainable Development Report.
Our internal safety standard defines safety-related fatality risks and minimum critical controls for their management.
We empower and expect our people to act (including by stopping work) when there is a potential or actual threat to health and safety. Our risk and event management system, Global360, supports our workforce in their efforts to proactively identify and report hazards and events. We investigate actual and potential significant events and hazards in accordance with our internal investigation protocol to capture learnings and improve controls.
Our people are protected against reprisal for reporting a hazardous situation or acting on a safety concern. These mechanisms are outlined in our Speak Up Policy and embedded in our safety standard.
Effective safety risk management depends on our workforce being adequately trained and equipped with the right competencies for the work they do.
Training frameworks are developed and regularly reviewed in accordance with our internal training standard. Job-related competencies are incorporated into our training and skills analysis, in line with our internal safety standard and as required by local laws. Skills matrices are developed and reviewed at least every two years, to identify capability development requirements, including training requirements for material safety risks.
Health and safety inductions are provided for all new employees and contractors, covering training on potential material health and safety exposures in the workplace.
We also engage with our people on health and safety issues through office- and operation-specific health and safety committees and through health and safety representative programs. These typically include peer-appointed representatives who promote health and safety improvement initiatives and assist with the management of safety-related issues and projects.
We empower and expect our people to act (including by stopping work) when there is a potential or actual threat to health and safety. Workers are protected against reprisal for reporting a work-related hazardous situation or acting on a safety concern. These mechanisms are embedded in our internal safety standard and outlined in our Speak Up Policy.
A culture that prioritises safety as a core value can enhance individual and collective contributions to safety performance.
Our LSED program includes safety leadership capability workshops and coaching, and has been delivered to over 1,500 leaders since its launch in FY23. The program is leader-led and locally facilitated, allowing for customisation as appropriate for the different locations and operating contexts of our operations, projects and offices.
While the program’s rollout is tailored, the overall objectives remain to form a common understanding of what it means to be a safety leader at South32, embed a consistent approach to safety risk management, and empower our people to speak up so that together we can prevent serious injuries and fatalities.
Read more about our LSED training program in our 2024 Sustainable Development Report.
Our internal security, crisis and emergency management (SCEM) standard defines minimum performance requirements and controls for responding to critical incidents and emergencies, with the aim of preventing or mitigating potential impacts to people, communities and the environment.
The standard requires that SCEM plans are developed, implemented, resourced and routinely exercised to mitigate material risks and to deliver a well-coordinated emergency response. Along with detailed SCEM plans, each of our operations has well-resourced emergency response and incident management teams with business continuity planning in place to manage potential events.
Our internal security, crisis and emergency management (SCEM) standard defines minimum performance requirements for managing security risks at our operations and projects, including conformance with the Voluntary Principles on Security and Human Rights (VPSHR).
We engage dedicated and professionally trained security teams to protect people and assets at our operations. Security providers at our operations must verify that they comply with the VPSHR. Additionally, private security providers must meet the requirements of the International Code of Conduct for Private Security Providers.
All externally contracted security providers are required to complete training aligned with the VPSHR every two years.
Health risks associated with our activities include exposure to airborne contaminants and hazardous substances, non-ionising radiation and communicable and infectious diseases.
Our approach to managing material health risks includes identifying material health hazards and setting thresholds for occupational exposure (Occupational Exposure Limits (OELs)) that are considered safe and are not likely to cause adverse health impacts. We implement a range of controls to prevent and reduce the risk of OEL exceedances. Employees and contractors have access to occupational health services, including medical surveillance and screening, to help to prevent and detect early-stage adverse health effects from occupational exposures.
We provide risk-based preventative health measures at our workplaces, including access to fitness facilities, general vaccines, and malaria and HIV/AIDS programs, where applicable. HIV/AIDS management is embedded in the occupational health processes at our Southern African operations and involves promotion of HIV counselling, testing and illness management. Positive cases are referred for treatment and we offer follow up as part of our chronic illness management program.
Psychosocial risk is the likelihood of physical or mental harm from exposure to psychosocial hazards, including poor work and workplace design, bullying, and harassment. We aim to eliminate or minimise these hazards across our operations and offices.
We are in the process of developing a new global psychosocial risk framework which aims to standardise the way that we identify, assess, and mitigate psychosocial risks across our business.
Our people are encouraged to raise awareness of, and encourage behaviours that support, health and wellbeing. Employees have access to our employee assistance program, which offers confidential counselling, and other mental health initiatives designed with the aim of supporting our people to feel safe and valued.
Sexual harassment is a workplace hazard that can cause both physical and psychological harm to our people. We continue to evolve our approach to proactively preventing sexual harassment and other inappropriate workplace behaviours. Read more in our 2024 Sustainable Development Report.
Community health risks are identified and managed in accordance with our internal health standard.
Community exposure to air emissions, such as dust, is monitored and managed at and in the vicinity of our operations. Our health standard defines the minimum requirements for monitoring programs when a potential community health risk is identified.
Our approach to managing ambient air quality includes:
Read more about our approach to managing air emissions in our 2024 Sustainable Development Report.